Compession Pressure
Inspection |
If the there is lack of power, excessive oil
consumption or poor fuel economy, measure the compression
pressure. |
1. |
Make sure the oil in the crankcase is of the
correct viscosity and at the correct level and that the battery is
correctly charged. Operate the vehicle until the engine is at normal
operating temperature. Turn the ignition switch to the OFF
position. |
2. |
Remove the engine
cover. |
3. |
Disconnect the injector extension connector
(A) and the ignition coil connectors (B).
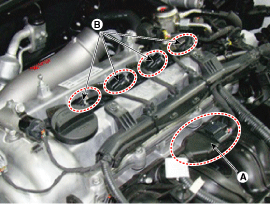
|
4. |
Remove the ignition coils (A).
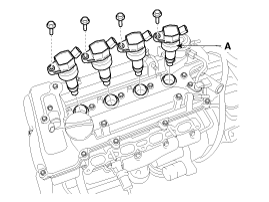
|
5. |
Remove the spark plugs.
Using a 16mm plug wrench, remove the 4 spark
plugs. |
6. |
Check the cylinder compression
pressure.
(1) |
Insert a compression gauge into the
spark plug hole.

|
(2) |
Set the throttle plate in the wide-open
position. |
(3) |
While cranking the engine, measure the
compression pressure.
Always use a fully charged battery
to obtain engine speed of 250rpm or
more. | |
(4) |
Repeat step 1) through 3) for each
cylinder.
This measurement must be done in
as short time as
possible. |
Compression pressure
Standard : 1225.83kPa (12.5kg/cm²,
177.79psi) (200~250 rpm)
Minimum : 1078.73kPa (11.0kg/cm²,
156.46psi)
Difference between each cylinder
:
98kPa (1.0kg/cm², 14psi) or
less
| |
(5) |
If the cylinder compression in one or
more cylinders is low, pour a small amount of engine oil into
the cylinder through the spark plug hole and repeat step 1)
through 3) for cylinders with low compression.
A. |
If adding oil helps the
compression, it is likely that the piston rings and/or
cylinder bore are worn or
damaged. |
B. |
If pressure stays low, a valve may
be sticking or seating is improper, or there may be
leakage past the
gasket. | | |
7. |
Install the spark plugs.
Tightening
torque :
7.8 ~ 9.8N.m (0.8 ~ 1.0kgf.m, 5.8 ~
7.2lb-ft)
| |
8. |
Install the ignition coil.
Tightening
torque :
9.8 ~ 11.8 N.m (1.0 ~ 1.2 kgf.m, 7.2 ~
8.7 lb-ft)
| |
9. |
Connect the injector extension connector and
the ignition coil connectors. |
10. |
Install the engine
cover. |
Valve Clearance Inspection And
Adjustment
Inspect and adjust the valve clearance when
the engine is cold (Engine coolant temperature : 20°C) and cylinder
head is installed on the cylinder
block. |
1. |
Remove the cylinder head cover. (Refer to
Timing system) |
2. |
Set No.1 cylinder to
TDC/compression.
(1) |
Turn the crankshaft pulley and align its
groove with the timing mark of the timing chain
cover.
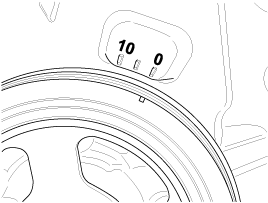
|
(2) |
Check that the marks of the intake and
exhaust CVVT sprockets are in straight line on the cylinder
head surface as shown in the illustration. If not, turn the
crankshaft one revolution (360°).

| |
3. |
Inspect the valve clearance.
(1) |
Check only the intake valves of the 1st
and 2nd cylinders and exhaust valves of the 1st and 3rd
cylinders for their clearance.
A. |
Using a thickness gauge, measure
the clearance between the tappet and the base circle of
camshaft.
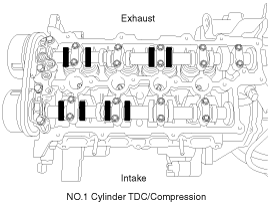
|
B. |
Record the out-of-specification
valve clearance measurements. They will be used later to
determine the required tappet for
adjusting. |
Valve
clearance specification (Engine coolant temperature :
20°C [68°F])
Limit
Intake : 0.17 ~ 0.23mm (0.0067 ~
0.0091in.)
Exhaust : 0.32 ~ 0.38mm (0.0125 ~
0.0149in.)
| |
(2) |
Turn the crankshaft pulley one
revolution (clockwise 360°) and align its groove with timing
mark of the timing chain
cover. |
(3) |
Check the intake valves of the 3rd and
4th cylinders and exhaust valves of the 2nd and 4th cylinders
for their clearance.
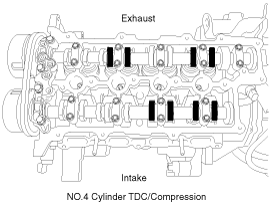
| |
4. |
Adjust the intake and exhaust valve
clearance.
(1) |
Set the No.1 cylinder to the
TDC/compression position. |
(2) |
Remove the timing chain. (Refer to
Timing system)
Put paint marks on the timing
chain links (2 places) that meet with the timing marks
of the intake and exhaust CVVT
sprockets. |
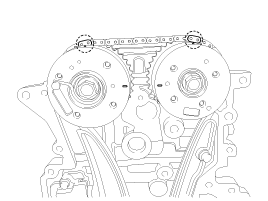
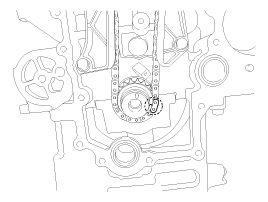
|
(3) |
Remove the camshaft bearing caps (A)
with the order below.
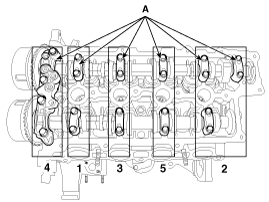
|
(4) |
Remove the intake camshaft
assembly. |
(5) |
Remove the exhaust camshaft
assembly. |
(6) |
Measure the thickness of the removed
tappet using a micrometer.
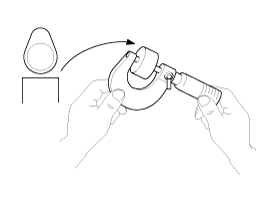
|
(7) |
Calculate the thickness of a new tappet
so that the valve clearance comes within the specificified
value.
Valve
clearance (Engine coolant temperature :
20°C)
T : Thickness of removed
tappet
A : Measured valve
clearance
N : Thickness of new
tappet
Intake : N = T + [A -
0.20mm(0.0079in.)]
Exhaust : N = T + [A - 0.25mm
(0.0098in.)]
| |
(8) |
Select a new tappet with a thickness as
close as possible to the caculated value.
Shims are available in 41 size
increments of 0.015mm (0.0006in.) from 3.00mm (0.118in.)
to 3.690mm
(0.1417in.) | |
(9) |
Place a new tappet on the cylinder
head. |
(10) |
Install the exhaust camshaft
assembly. |
(11) |
Install the intake camshaft
assembly. |
(12) |
Install the camshaft bearing caps with
the order below.
Tightening torque :
1st step
M6 bolt :
5.9 N.m (0.6 kgf.m, 4.3
lb-ft)
M8 bolt :
9.8 N.m (1.0 kgf.m, 7.2
lb-ft)
2nd step
M6 bolts :
11.8 ~ 13.7N.m (1.2 ~ 1.4kgf.m,
8.7 ~ 10.1lb-ft)
M8 bolts :
18.6 ~ 22.6N.m (1.9 ~ 2.3kgf.m,
13.7 ~ 16.6lb-ft)
|
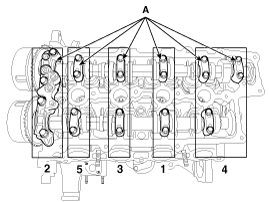
|
(13) |
Install the timing chain. (Refer to
Timing system) |
(14) |
Turn the crankshaft two turns in the
operating direction(clockwise) and check that the marks of the
intake and exhaust CVVT sprockets are in straight line on the
cylinder head surface.

|
(15) |
Recheck the valve
clearance.
Valve
clearance (Engine coolant temperature :
20°C)
[Specification]
Intake : 0.17 ~ 0.23mm (0.0067 ~
0.0091in.)
Exhaust : 0.22 ~ 0.28mm (0.0087 ~
0.0110in.)
| | |